With help from a massive metal grinder, a dairy makes energy from food waste
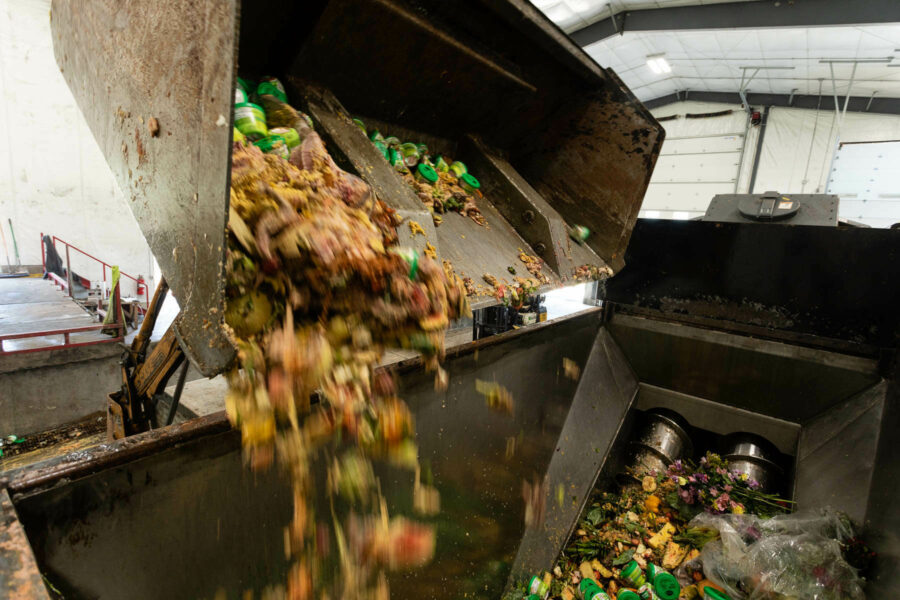
For farmers facing economic challenges, investing in sustainable technologies usually benefits their business as well. Saving energy saves money, after all.
Reinford Farms, a 700-cow dairy operation in central Pennsylvania, is no exception.
“With the dairy industry the way it is, we’re looking at other ways to kind of help us stay more viable economically,” said Brett Reinford, who works alongside his siblings and father, focusing mostly on the business side of the farm. “And sustainability is a no-brainer investment for us to do.”
In 2008, Reinford Farms installed a methane digester, which allows them to generate electricity and heat from manure. Though when Reinford first pitched the technology to his father, it was to solve a different problem.
“I know at the time he was like, ‘Man, we’ve got to do something about the smell around here,” Reinford said. Reducing the smell of manure is something solar panels or wind turbines can’t accomplish, but a methane digester can.
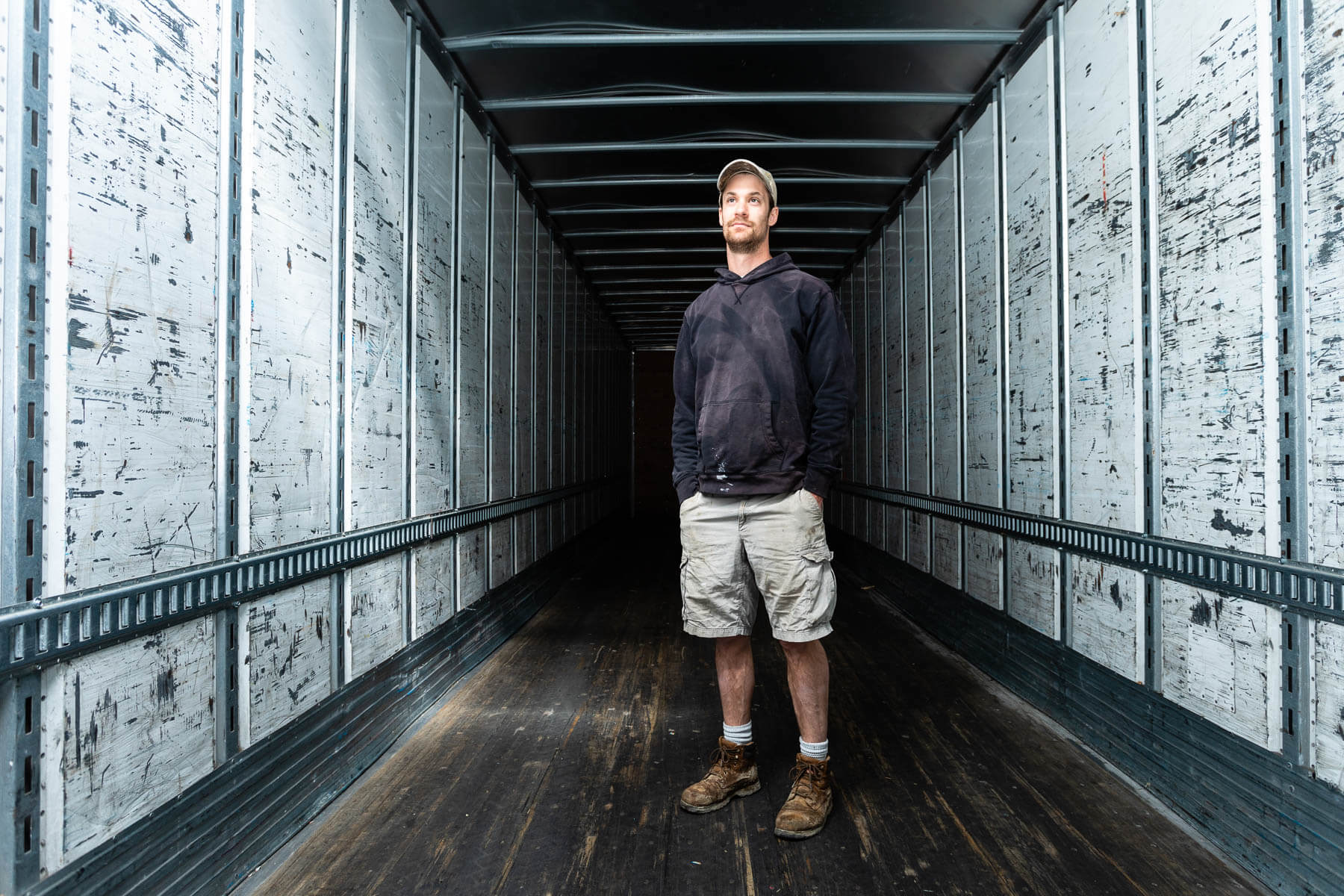
Methane digesters work by controlling the decomposition of waste—usually manure. Digesters trap methane that is then burned as an alternative fuel and produce nutrient-rich solids that can be used as fertilizer. The farm discovered more benefits after another farmer visited and asked the Reinfords what they were doing with the heat coming off the digester. They didn’t have an answer.
“Then we started looking at the heat side of the motor and we thought, ‘Well we can heat our hot water with it, we can dry our corn with it, we can heat our shop, we can heat our house,” Reinford said. “In doing that, we actually don’t have to purchase any fossil fuels for heating sources.”
The farm now sells electricity from the digester, as well as using separated and dried manure solids from the process as healthy bedding for its cows.
Just weeks after installing the digester, a hauler for Walmart called the farm and asked if Reinford was interested in feeding it their organic waste alongside the farm’s manure. After consulting an expert at Penn State University, the farm agreed. They took in waste for about ten years, diverting it from landfills. But they noticed that some deliveries included larger pieces of trash that were making it into the manure storage pit, which receives the waste for the digester. And for the last four of those years, they were accepting packaged food that took at least five workers to process. One hot summer, the farm processed 30 semi-truck loads by hand—and reached a tipping point.
“We opened every single clamshell, lettuce thing, every single bag, just an incredible amount of labor and no one wanted to do it anymore,” Reinford said.
So, in late 2016, Reinford Farms decided to invest in a room-sized machine called a depackager, one of only a handful that are operating at farms across the country. While it took five workers a-day-and-a-half to process one truckload of food waste, the depackager can now handle that amount in as little as an hour.
When pallets of food waste come into a specially designed building on the farm, workers do the initial unboxing and bailing of cardboard, which is recycled. After that, whole cans, jugs and plastic bags are no match for the depackager, which grinds them between rapidly spinning metal arms, separating the organic waste from its containers.
“It gets [cans] pretty clean,” Reinford said. “Clean enough that the recycler says we don’t need to do anything to it.”
The farm takes in waste from over a dozen clients in a radius of about 75 miles from the farm, including a large food supplier and several grocery stores, including Wegmans Food Markets.
“Everything we get is inedible,” Reinford said. “Wegmans does a great job of donating a lot of their food to food banks.”
In March, 2020, a new methane digester—four times the size of their first—increased the farm’s capacity as well as the amount of electricity it can sell back to the power grid—enough to power 600 homes. The farm also hopes to make its depackager available for other farms in the area that have methane digesters but aren’t able to accept packaged food waste.
Reinford, who worked for a couple years at a software company before deciding he didn’t like the corporate world, said that the adoption of sustainable technologies like the digester and depackager was what lured him back to the family farm in the first place. He hopes, for example, that technological developments will eventually allow the farm to separate most of the excess nutrients from its wastewater.
“From a sustainability standpoint we love looking at waste and figuring out how to make it a resource,” Reinford said.
Comments
There are no comments.
Thank you!
Your comment has been received. Before it can be published, the comment will be reviewed by our team to ensure it adheres with our rules of engagement.
Back to recent stories